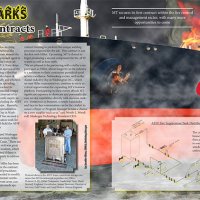
MT Sparks New Contracts
Developed in the 1960's, aqueous film-forming foam (AFFF) has been used by branches of the U.S. armed forces and fire departments around the world. This highly efficient fire suppressant agent is used to control fires on some of today's most advanced military vehicles including U.S. Navy ships. The...